- Furnace Safety Supervision System
- Ignition Control System
- The Ignition And Combustion Equipment
- Energy-saving Combustion System
- Combustion Test Bench
- PLC Programmed Control System
- Industrial Television Monitoring System
- Flare System
- Intelligent Online Soot Blowing System
- Acoustic Gas Temperature Measurement System(SEI)
- Compressor Optimization Control System(CCC)
http://www.nendar.com
Phone:0516-83899666
postcode:221008
E-mail:xznengda@126.com
Address:Hardware district 1 11,National University Science Park of China University of Mining and Technology,Xuzhou,Jiangsu,China
Acoustic Gas Temperature Measurement System(SEI)
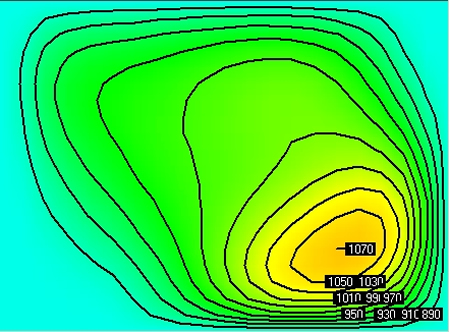
1.Outline
The basic requirements of industrial boilers burning to build and maintain a stable flame, in a typical Tangentially fired boiler, the four corners of the combustion conditions caused by the irrational organization uneven combustion, flame center deflection, whitewashing, etc. leading to the furnace flame coke, blast furnace, furnace fire, explosions and other important reasons furnace run accident. Therefore, the diagnosis of coal-fired boiler burning a very important practical significance.
Here to introduce you to a current world's most advanced industrial boiler furnace temperature field measurement method --- acoustic gas temperature measurement system.
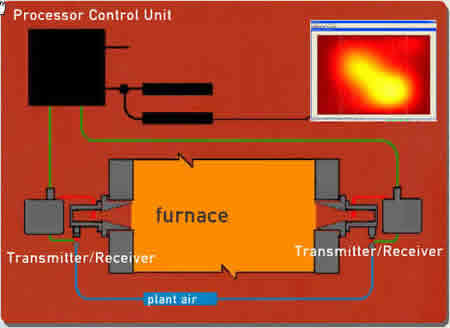
Acoustic gas temperature measuring system to benefit from the sound, electricity, on advanced signal processing techniques to provide a continuous, accurate, real-time, non-invasive automatic measurement of the thermal processing or combustion gas temperatures. Sonic gas temperature measurement system is a complete system for permanent use various boilers, stoves.
Acoustic measurement system capable of measuring the gas temperature in one or two separate arrays of up to 24 average temperature of the gas passage for the gas temperature distribution in the plane. Measuring range from 0 ℃ to 1927 ℃. Temperature data sonic gas temperature measurement system can be sent to step control system factory (DCS), data acquisition systems (ADS), the computer display or storage. Temperature time trends can be operated by a computer or DCS operation acoustic gas temperature measuring system software. Isothermal temperature profile contour maps, the average temperature of flat sub-region and other data is readily available in the sonic gas temperature measurement system software.
Sonic gas temperature measurement system designed to provide boilers, air stoves, furnaces and other combustion thermal processing environment two-dimensional plane of the spatial distribution of temperature, color isothermal wireframes, time and temperature trends, regional temperature color chart for plant or 0-20 mA process control signal system.
2.Works
The basic principles of acoustic gas temperature measuring system is based on the speed of sound in the gas in accordance with a temperature change as a function of the fact, and further along the acoustic path is affected by the gas component. These relationships are described by the following equation: c = d/t=sqrt[rRT/M] c = d / t = sqrt [rRT / M] Here r is the specific heat of gas at atmospheric pressure than the hot gas is a constant;Gas molar weight M Kg / mol) R is the gas constant (8.314J/K-MOL) T absolute temperature Calvin).
The sound source (transmitter) is mounted in the side of the furnace or boiler, the microphone (receiver) is mounted on the rim, a sound signal transmitter for transmitting and receiving device can be detected. Because the distance between the transmitter and the receiver is fixed, measuring the propagation time of the sound signal to allow a known average gas temperature is calculated in accordance with the path between the transmitter and the receiver. Installation indicate:
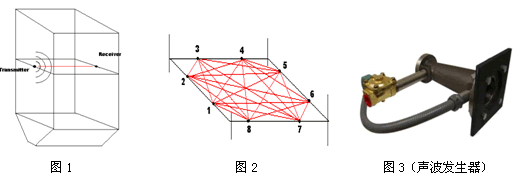
Sonic gas temperature measurement system can provide a two-dimensional plane temperature distribution, providing accurate real-time temperature data for the production of control, with real-time alarm function, easy DCS interface.
Therefore, it has the following advantages:
3.1 Monitor hot spots and protect the furnace and the workpiece, reducing unplanned downtime, to achieve safe production
Because the combustion process, the acoustic gas temperature measurement system provides accurate, real-time temperature profile data and alarm functions for us, for the control of temperature provides valuable data.
Based on these data we can monitor whether the direct flame water wall tube erosion phenomena, adjust the position of the flame to avoid direct water wall tube erosion, water wall tubes to avoid damage, improve circulation and improve operational efficiency furnace.
Monitoring data to identify whether the low-temperature region is not working properly, or clogging of the burner, thereby improving the air / combustion ratio, fuel injection or combustion improving the distribution, mixing and circulation furnace, heat distribution and improved operating efficiency. Extended service life and reduce heat loss.
3.2 Saving energy, reducing emissions of fly ash and soot
Using sonic gas temperature measurement system, so that we can be controlled by adjusting means for changing a reasonable proportion of fuel and air, and other factors in the furnace under the burning conditions of reasonably optimized to achieve optimal combustion (complete combustion), achieve energy saving, reduction of fly ash and soot emissions, the purpose of reducing operating costs.
Boiler efficiency is also dependent on good heat transfer rate between the fire and the boiler pipe, when the pipe is gradually filled with soot, cause heat absorption pipe is reduced, so that the furnace exit gas temperature rise efficiency of the boiler decreases. Continuous monitoring of the stove outlet gas temperature and power output, can alert the operator on the basis of real-time information on start blowing soot.
It has been found: the loss of soot blowing, according to the different types of coal, and the operator can vary widely. Excessive use of the device caused by soot blowers cost burden. This cost is due to the use of electricity caused by the power generation sector. If the steam is blowing (soot) media, then the available steam generator steam turbine will be reduced, resulting in reduction of power generation.
After estimating a 415MW (installed capacity) power plant, the annual cost of 8,000,000 soot blowing and 16 million yuan (RMB) between, not including boiler efficiency losses. Soot blowing optimization strategy is very valuable.
3.3 The furnace or boiler can achieve automatic control function
This real-time temperature data is used to adjust the side wall burners, burner and the bottom surface is sprayed into the air (air register) to eliminate hot spots and cold spots, until around the three-dimensional heat flux tube to achieve uniform work to minimize nitrogen dioxide (NO2 ) / sulfur dioxide (SO2) emissions, prevent waste chemicals and power.
Many furnaces and boilers, the reason can’t be automatically controlled, the key is not accurate because the plane temperature distribution of real-time data. Sonic gas temperature measurement system is to solve this critical problem. DCS interfaces easy, accurate real-time temperature data for the automatic control of the stove lay a solid foundation.
3.4 To extend the life of the furnace, to reduce consumption costs, save money
Sonic gas temperature measurement system is a one-time investment, non-intrusive measurement instruments for permanent use, its use, on the one hand so that we can replace thermocouple temperature measurement devices and the like, there is no long-term consumption of these components, saving the expenses. On the other hand, allows us to avoid the over-burning furnace, extending the life of the furnace. While also avoiding the losses due to over-burning furnace shutdown caused damage.
3.5 Reduce scrap, improve product quality, reduce production costs
In thermal processing, the user can measure the temperature of the gas temperature acoustic data provided by the system, proper control of oven temperature and the temperature distribution for the production of qualified products provide reliable protection technology, improve product quality and production efficiency, but also reduce the cost of production . By controlling device, reasonable changes in temperature distribution, the temperature is controlled within a reasonable range, the temperature is too high or too low to avoid local over-burning phenomenon, which could be avoided due to the over-burning stove and products arising damage, reducing substandard goods. To provide a reliable guarantee safe production.
3.6 Recall the accident
The furnace combustion conditions recorded as files provide accident investigation, for operating personnel combustion diagnosis has important practical significance.
3.7 The user interface can be set to a variety of operating screen
3.8 Accurate and reliable, error of less than 1.5%
Engineering heater control circuit.
3.8.1 Features
-Real gas temperature measurement -Non-intrusive, fully automatic -Serial output can be set Ethernet -Flexible configuration -Easy to install, easy to start -Can be run on any fuel cell -Cost-effective, reliable and mature technology
3.8.2 Application
-Organic process heaters -Ossil fuel utility power plant boilers, chemical recovery, waste generation -Industrial furnaces process monitoring / control -Minimum temperature from the amount -Other industrial thermal engineering
3.8.3 Effect
-The impact from thermal stress by balancing the protection of the combustion tube -Reduce downtime and loss of opportunity passive -Improve operational efficiency, improve heat flux -Reduce NOx emissions by eliminating excessive temperature conditions -Minimum of coking phenomenon -Provide accurate data for the real-time process gas temperature control
BOILERWATCH MMPII acoustic pyrometer is an advanced industrial installations, it is capable of heater or boiler to provide fully automated high temperature combustion gas measurement and fuel adjustment control. For the hot gas itself is completely non-invasive, its working principle is proportional to the temperature of the gas has adopted a system based on sound wave propagation velocity with it. Acoustic source and receivers disposed in the outer wall of the heater or boiler, a low intensity acoustic signal is emitted and through the stream. Since the distance between the sound source and the receiver is known and fixed, through an accurate measurement of the propagation time of the acoustic signal, the average temperature of the acoustic channel can be calculated. BOILERWATCH MMP II system can have a variety of configurations. As the temperature measurement can be achieved up to 24 channels, the system is configured to give not only provide spatial temperature distribution, or independent temperature measurements, and be able to combine the two. BOILERWATCH MMP II system is easy to install, start-up and operation authorization.
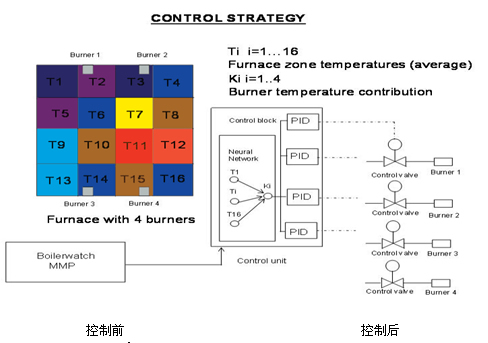
-Transmitter Receivers: Minimum 6 Maximum 16
-Measuring range: 35 to 3500 F (0 to 1927 C)
-Temperature Units: Imperial or Metric ( F or C)
-Resolution: 20 m long channel during 2000 F (1093 C) for 12 F (6.7 C)
-Accuracy: 1.5% or less
-Measuring time: 5 seconds / channel
-Data output: RS-232 / RS-422 and multi-format,modem Is equipped with a standard built-in modem for
remote monitoring
-Alarm output: hardware fault indication output and other user-defined alarm signal
-AC Power Input: 100~240 VAC, 50/60 Hz, single phase, 6.0/3.0 amps, auto-sensing
-Sonic Generator: Inflatable sound generator, use the factory GM air
-Sound source pressure: 60 - 120 psig (5.0~8.3 Bar)
MMP II PCU MMP II PCU
-Ambient air temperature: + 130 F (54 C) the highest, avoid direct sunlight
-structure: 30 in. H x 24 in.W x 12 .D (762 x 610 x 356mm) * NEMA 4 steel
-Weight: 110 lb (50 Kg)
Waveguide device (Waveguide)
-Material: Stainless steel 316L -Specifications: 7.88 in. flange diameter (200mm), the length of 12.78 inches (325mm) -Flanges: According to ASTM standard 3-inch 150 lb pipe flanges - (Please open the specific contact us for your heater or boiler) -Weight: 26 lb (11.8 Kg)
Ambient temperature
-Flange: +450 F (+232℃) max -Surrounding gas: +130 F (+54℃) max
3020TR transmitter box
-Ambient gas temperature: + 140 F (60℃) max, avoid direct sunlight -Case: 13.5 inches high x 11.4 inches wide x 5.1 inches deep (343 x 288 x 130mm) * NEMA 4 fiberglass or steel -Weight: 14 lb. (6.4 Kg) -Warranty Period: 1 year (standard)